Introduction
Problem:
Children are not receiving the nutritious meals they require in school due to lack of funding and a restrictied supply of nutritious vegetables for the GSFP. Contracted calerers are unable to get proper pay for their services in a timely manner pushing them into using shortcuts and compromising the quality of food served to school children.
Proposed Project:
Design a low-cost hydroponic farming system for pilot school in Kumasi, Ghana to supplement food supply.
Products | Benefits | Drawbacks |
Commercial Hydroponics |
|
|
Low-Cost Hydroponics |
|
|
HydroGrow |
|
|
Table 1: Existing Market Comparison
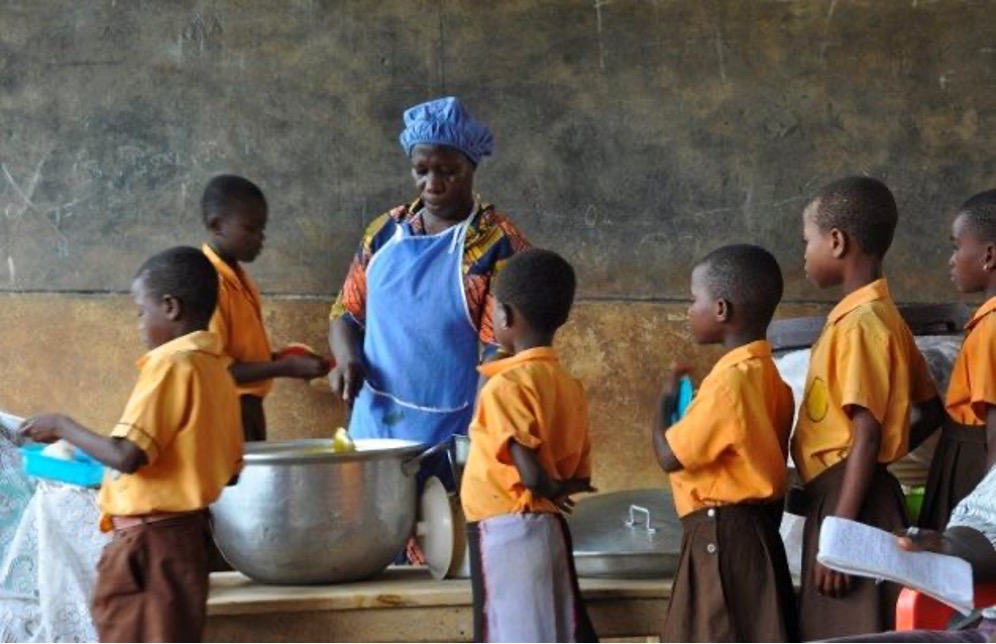
Objectives
Parameters for Project Design:
- Low maintenance for end user
- Usability with minimal agricultural background
- Reproducible and scalable systems
- Housing in shipping container to mimic greenhouse
- Compatible with unstable power supply
- Automation via electrical systems
Materials & Methods
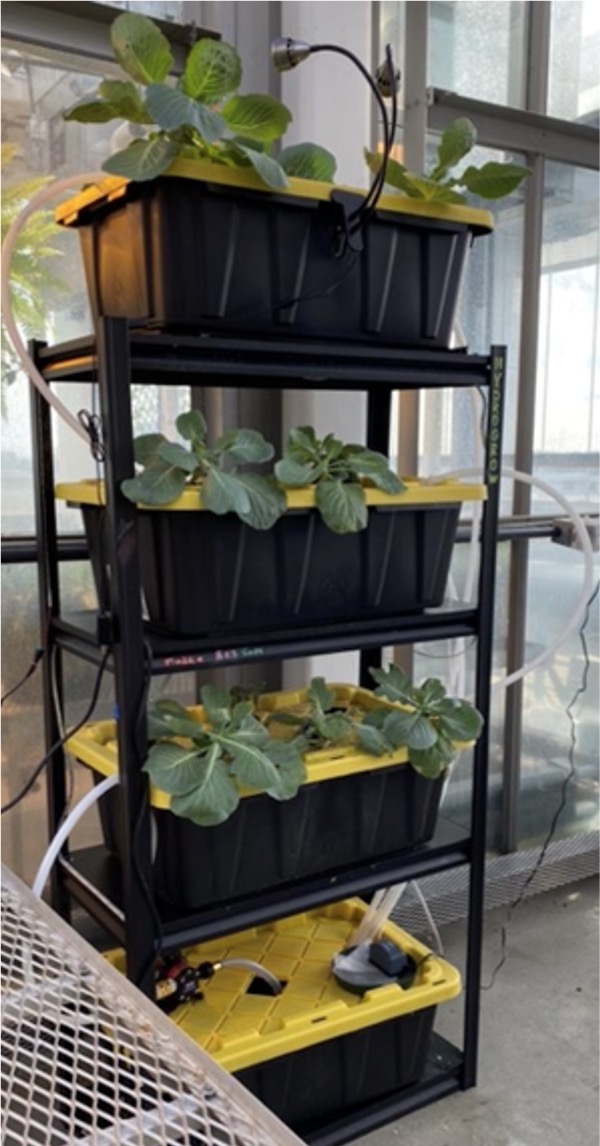
Stack design:
- Clip on grow lights and LED strips lights on underside of shelves
- Holes cut into each bin to fit vinyl tubing, sealed with waterweld epoxy
- Bottom bin: reservoir with water & nutrients
- Transfer pump pulls from reservoir bin to circulate medium to all growth bins
- Growth bin; Cabbage holder with nutrient medium
- Drainage tubes: water doesn't overflow during transfers from reservoir bin
Shipping container details:
- 2 rows with 28" space between
- 3 units high (1 stack)
- 11 stacks long (22 total stacks)
- 396 plants in rotation
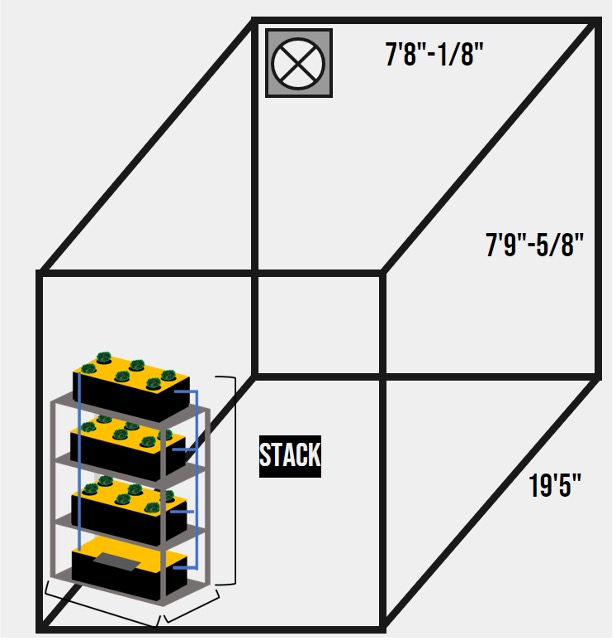
Data presentation:
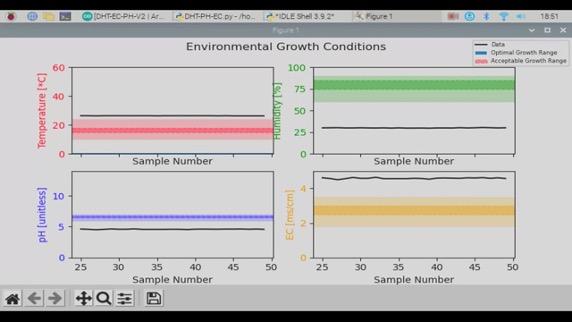
User will see environmental conditions visually displayed on screen connected to Rasberry Pi. User will see what conditions to change for optimal growth.
Results
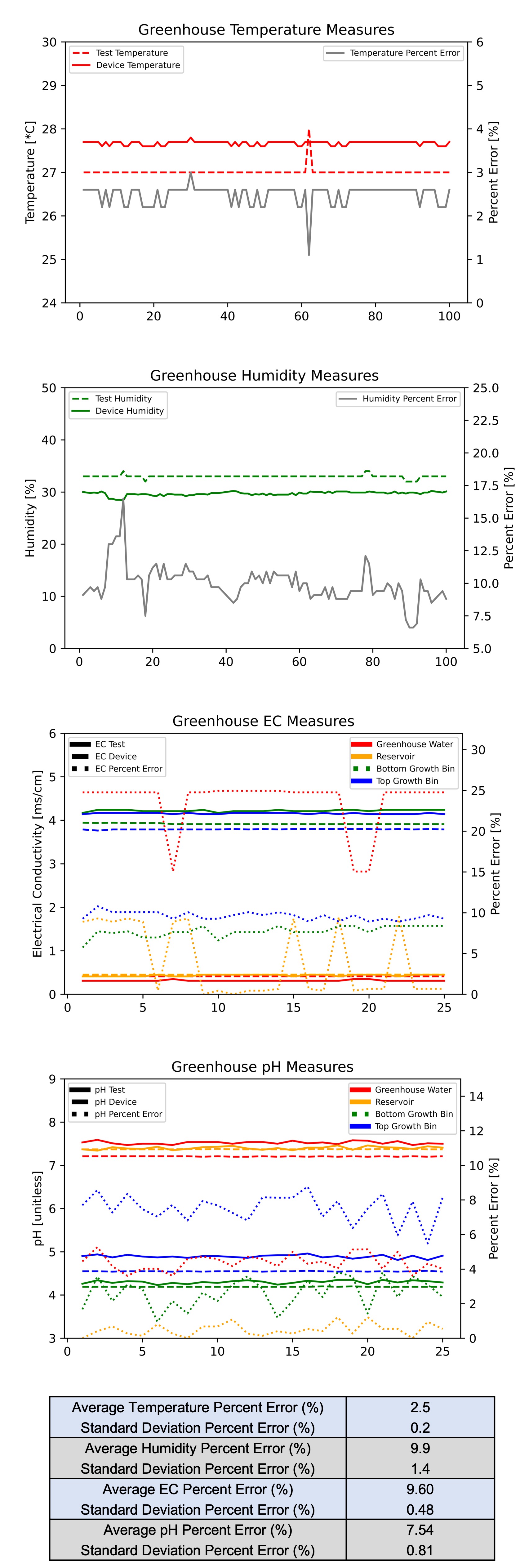
Data collection:
Data samples were collected with the DHT@@, EC probe, and pH probe sensors, through the Arduino Uno. Data was transmitted to a Raspberry Pi for data processing and display via USB.
Greenhouse data samples were collected for the system of the ambient environment, greenhouse water supply, reservoir bin, bottom growth bin, and top growth bin. The plots on the right demonstrate the respective measures and their percent errors.
Data Analysis:
Percent error measures are greater than the acceptance threshold of + 5% which demonstrates lower than expected accuracy. Standard deviation measures display consistent data samples, which demonstrates high precision.
Water Circulation Timing:
- Process: 30 seconds on followed by 4 minutes off
- Repeat 5 times to raise water levels and circulate nutrients
Manual Creation:
- Provide instruction on building and operating the hydroponic system
- Answers questions the user might have
- Supplies a diagnosis and treatment guideline fro plant diseases and pests
- Shows the user how to interpret the display
- Defines the hydroponic cabbage growth timeline
Current Cabbage Growth:

Conclusions
Positive Outcomes:
- Project establishes an effective proof-of-concept for a hydroponic project that could be deployed to pilot and other locations
- Sustainable and scalable business model has been well thought out as a result of participation in teh GW New Venture Competition
- Plant growth, with additional unexpected challenges, have been thoroughly documented in user manual for future research and work
Current Problems:
- By taking a general approach for data collection in each growth bin, differential treatment of individual plants is neglected for different growth stages
- The current epoxy is inefficient in preventing leaks and should be changed to a new product or different method
- Aphids and other pests/diseases continue to damage the cabbage growth process
Future Improvements:
- Need more finely tuned calibration of sensors to increase assurance of measurements displayed
- Once sensors are finalized, the printing and programming of the dispensers can begin
- Change heights of the shelves to optimize space for cabbage heads
References
R.K. Nyarko, "School feeding program sends strong warning to caterers who are not cooking for children," MyJoyOnline.com, 06-Aug-2021. [Online]. Available: https://www.myjoyonline.com/school-feeding-program-sends-strong-warning-to-caterers-who-are-not-cooking-for-children/. [Accessed: 10-Apr-2022
"Home," Arduino. [Online]. Available: https://www.arduino.cc/. [Accessed: 16-Feb-2022].
Raspberry Pi, "Teach, learn and make with Raspberry Pi," Raspberry Pi. [Online]. Available: https://www.raspberrypi.org/. [Accessed: 10-Feb-2022].
"Adafruit Industries," GitHub. [Online]. Available: https://github.com/adafruit. [Accessed; 20-Feb-2022].
"DFRobot," Github. [Online]. Available: https://github.com/DFRobot. [Accessed: 20-Feb-2022.
"Visualization with python," Matplotlib. [Online]. Available: https://matplotlib.org/. [Accessed: 09-Feb-2022].
Acknowledgements
BME Capstone Team: Professor Hyung Sok Choe, Mariia Sidulova, Magdeline Schoonover
SEH Greenhouse Team: Rachel Canalichio
Ghana Subject Matter Experts: Edward Amoah Idun, Andrews Idun